ZetaLiner:
The Oregon Aero ZetaLiner consists of Confor Pal
visco-elastic foam sewn into washable, wear resistant Orthonice (inside)
and Velsap (outside) fabric. The liner is held in place with the aid of
velcro hook-tabs that are glued to the energy absorbing styrene liner. Impact testing of
an HGU-55/P helmet conducted by the USAF in 1999 showed that the ZetaLiner gave
a 25-35% reduction in impact loads when compared to the Gentex TPL® liner. The
ZetaLiner was introduced in US Army as an special-fitting alternative for
people who could not use a TPL® liner due to their head form, and the USAF and
Navy are gradually introducing it for special applications in Special Operations and for
the Joint Helmet Mounted Cueing System HGU-55A/P helmet. |
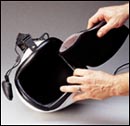
|
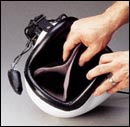
|
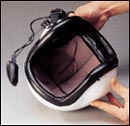
|
ZetaLiner
liner folded and ready to insert into helmet.
Photo© Oregon Aero |
ZetaLiner
liner positioned in helmet. Photo© Oregon Aero
|
ZetaLiner
liner finstalled and helmet is ready to use.
Photo© Oregon Aero
|
|
|
|
TPL®- Thermo
Plastic Liner: The Gentex TPL® system uses layers of firm plastic that
is best described as hard bubble wrap. The "bubble layers" are covered with a
soft, black "sock." This sock not only provides comfort to the wearer but also
holds the liner in place with the aid of four velcro tabs that are glued to the energy
absorbing styrene liner. TPL®s can be custom fit to the wearer by heating the
liner and forming it to the head, but they can also be used as they come. A flight helmet
can be fitted by adding or removing layers of the plastic bubbles. The TPL®
was introduced as a light-weight, easy-to-fit, environmentally friendly alternative to the
custom fit urethane foam liners. Used in a range of current flight helmets including
HGU-55/P, HGU-68/P, SPH-4, SPH-5, and HGU-84/P. |
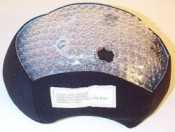
|
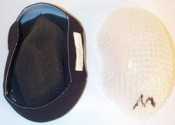
|
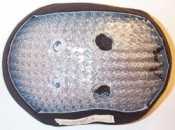
|
TPL®-liner showing the bubble layers with vent holes
Photo ©Trey Turner |
TPL®-liner where the bubble layer has been separated from
the sock
Photo ©Trey Turner |
TPL®-liner seen from above
Photo ©Trey Turner |
|
|
|
Form Fit V-TEC:
The V-TEC liner is a helmet shell liner that is form-fit and constructed from a one-ply
fibreglass backing, a leather covering and a comfort pad. The leather covering and comfort
pad are cemented to the fibreglass backing, The fibreglass backing has two holes for
introduction of foam chemicals. The VTEC is placed on the user's head, a helmet shell with
a hole cut in the top is put on and pulled down. A special warm expanding foam is poured
in the holes in the top of the liner and a mold is made of the wearer's head. When
properly fitted the liner absorbs impach energy and makes the helmet stable and
comfortable. The aircrew member wears a perspiration-absorbing cotton skullcap to extend
the life of the liner. The VTEC was widely used during the 1980s by US Navy crewmembers.
Most commonly found in HGU-33/P and HGU-45/P fighter helmets based on the PRK-37/P helmet
shell, and HGU-54/P, HGU-59/P and HGU-64/P helicopter helmets based on the PRU-45/P helmet
shell (also used in the SPH-3C helmet). The liner used in the PRK-37/P helmet shell is
designated PRU-39A/P while the liner for the PRU-45/P helmet shell is designated PRU-43/P. |
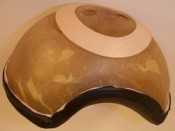
|
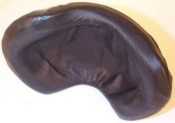
|
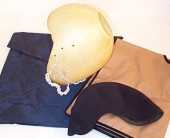
|
PRU-39A/P liner showing the fibreglass top with its two holes for pouring in
the urethane foam and venting
Photo ©Trey Turner |
PRU-39A/P liner seen from below showing the leather pad area
Photo ©Trey Turner |
Custom fitting helmet shell with hole in the top for pouring the urethane
foam into the PRU-39A/P liner
Photo ©Trey Turner |
|
|
|
PRU-39/P Custom Fit
Urethane Foam Liner: The PRU-39/P is a helmet shell liner that is a form-fit,
foam-in-place type assembly. Unlike the majority of other liners the PRU-39/P does not
require a separate energy absorbing urethane foam liner in the helmet shell. It provides
both energy absorbtion and comfort for the wearer. The PRU-39/P consists of a rigid
urethane foam liner molded to fit the aviator's head. The KMU-439/P Liner Mold Kit is
positioned on the crewmember's head, and foam chemicals are injected into it. The liner is
finished with a soft urethane foam comfort pad and leather covering. When properly fitted,
the liner provides impact energy absorption, helmet stability, and comfort. The custom fit
urethane foam liner can also be made in a remote location using a plaser or wax mold of
the user's head. The PRU-39/P and similar custom fit urethane foam liners were widely used
from the mid-1970s through the 1980s by US Air Force and US Navy crewmembers. Most
commonly found in HGU-26/P, HGU-33/P and HGU-55/P. The PRU-39/P designation refers
specifically to the liner used in the Navy PRK-37/P shell (HGU-33/P, HGU-45/P etc.) |
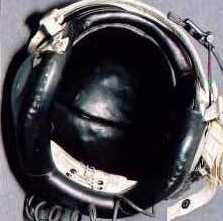 |
|
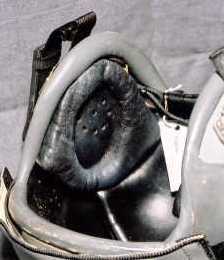
|
Custom fit polyurethane foam liner in HGU-26/P.
Photo ©Steen Hartov
|
|
Custom fit polyurethane foam liner in HGU-55/P helmet. The edge is trimmed to
match the profile of the 'elephant's ear' earphone pads.
Photo ©Steen Hartov |
|
|
|
Percentile Liner:
Percentile helmet liners are leather covered urethane foam liners but they should not be
confused with the custom fit urethane foam liners. The percentile liners are made in six
U.S. Air Force standard head sizes determined statistically based on measurements made on
actual aircrew. The six sizes fit the 5-, 25-, 50-, 75-, 95- and 98-percentile of the head
sizes. They are made in the same way as the custom fit urethane foam liner except that a
standard size head mold is used instead of the individual user's head. |
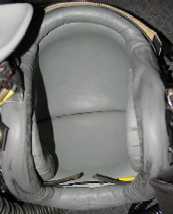
|
|
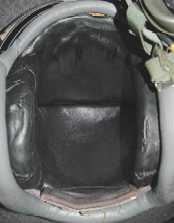
|
Percentile liner in an HGU-55/P helmet
Photo ©Kirk Sunley |
|
Percentile liner in a Gentex HALO helmet
Photo ©Kirk Sunley |
|
|
|
Fitting Pads:
This is a very common type of liner system. The helmet shell must be equipped with an
energy absorbing styrene liner before mounting the fitting pads. The leather fitting pads
either have self-adhesive backing or are mounted on self-adhesive velcro strips attached
to the styrene liner. They come with several layers of sizing pads so you can customize
the fit to some extent. The fitting pads were introduced in the late 1950s in the US Navy
APH-5 helmet and derivatives. Used on a range of helmets including the APH-5, APH-6,
AFH-1, HGU-2/P, HGU-2A/P, HGU-26/P, and HGU-34/P series flight helmets. |
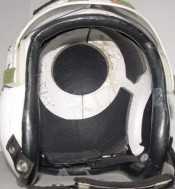
|
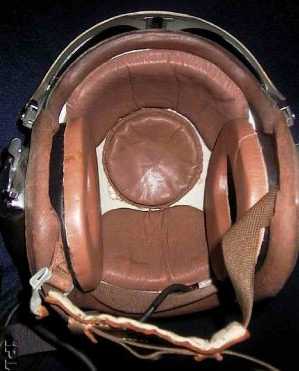
|
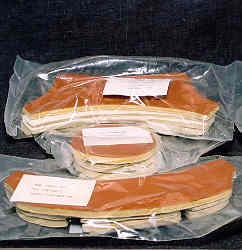 |
Black fitting pads mounted on the white polyurethane energy absorbtion liner
in an HGU-34/P helmet. Liner and pads together are designated PRK-40/P
Photo ©Trey Turner |
Liner pads in an APH-5 helmet
Photo ©Steen Hartov |
Set of liner pads for an HGU-26/P helmet
Photo ©Steen Hartov |
|
|
|
Strap suspension
assembly: The strap suspension assembly used to be a very universal type of liner.
In order to get the full protection from the suspension assembly the helmet shell must
also be equipped with an energy absorbing styrene liner. The suspension assembly is
popular because it allows air to flow over the wearer's head, providing comfort. During an
ejection, however, this air flow could rip the helmet off the pilot's head. Another
disadvantage is that it can easily provoke 'hot-spots' if it is not fitted correctly. This
style of liner was introduced in US flight helmets in the late 1940s but was replaced by
fitting pads in fast-mover helmets in the late 1950s. The strap suspension assembly
continued in service in slow-mover helmets like the SPH-3B, SPH-4 and APH-7, and it was
also used in certain export versions of the HGU-2-series helmet. |
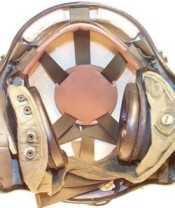
|
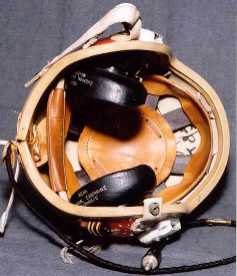 |
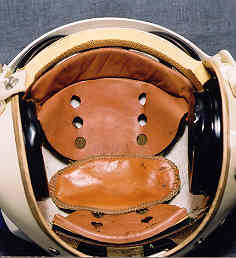 |
Strap suspension assembly in an SPH-4 helicopter helmet
Photo ©Trey Turner |
Strap suspension assembly in a P-4 helmet
Photo ©Steen Hartov |
Strap suspension assembly in an HGU-2A/P(G) helmet.
Photo ©Steen Hartov |
|
|
|
Sierra foamed
liner: The Sierra foamed liner uses foam rubber to provide noise reduction
and contours to the wearer's head for comfort. It is installed inside the standard energy
absorbing polyurethane foam liner and is covered with a washable cloth liner. Apparently
it was used mostly for special applications where noise attenuation was at a premium. |
|
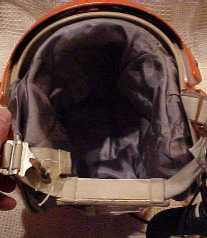
|
|
|
Sierra foamed liner in an Australian Air Force APH-6/A helmet used in Beavers
on the Antarctic.
Photo ©Howard Jones |